Drywall Repair is a common home improvement project. Knowing how to perform this task can save time and money for homeowners.
Minor blemishes like nail or screw holes, and hairline cracks can be easily repaired with spackle and paint. Larger cracks and stains can indicate structural issues and should be addressed promptly. Contact Professional Home Repair now!
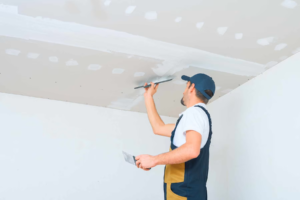
Small, straight cracks along doorways and windows are common in drywall and usually don’t indicate a structural problem. They could be caused by normal settling of your home or by drywall panels that weren’t taped or properly supported when initially installed. These cracks may also be the result of water leakage. In this case, you’ll want to address the source of the leak before trying to repair the drywall.
Larger cracks in drywall can be more problematic. If they’re not addressed immediately, these cracks can lead to mold and mildew, and higher energy bills. They may even indicate a more serious issue such as a foundation problem that needs to be fixed before continuing with the drywall installation.
Regardless of the cause, these larger cracks are best left to a professional drywall expert. Attempting to fix them yourself risks papering over the cracks and may allow them to return or worsen.
For small holes and isolated cracks, you can often get away with using a do-it-yourself drywall patch kit. Start by cleaning the area and removing any loose paper or gypsum. Then, apply a thin layer of drywall joint compound with a putty knife and smooth it. Use a sanding sponge or sanding block to finish sanding the surface until it’s smooth and blends with the rest of the wall. Add a second coat of joint compound, sand again, and then paint as needed.
Hairline cracks that develop in a series of lines across your walls or ceiling are typically caused by natural settling of the house. These cracks are common in new homes and shouldn’t be a concern unless they continue to occur over time. However, they’re more likely to indicate a problem if you have a lot of them or if they appear near doors and windows. These cracks are the result of a buildup of pressure that’s being put on the drywall and may be more difficult to repair. If you notice any of these hairline cracks, have a professional inspect your home and take appropriate steps to address the issue.
Holes
Regardless of their cause, holes can lead to further damage and should be repaired promptly. While small holes and nail pops are relatively easy to repair with spackle and paint, bigger problems require a more thorough assessment to determine underlying issues that need to be addressed. Moisture damage, for example, can cause drywall to deteriorate and even collapse. This is often a sign of serious plumbing or structural issues that need to be resolved before proceeding with repairs.
The size of a hole determines how it should be repaired, and there are several methods that can be used depending on the situation. For holes that are smaller than a doorknob, for instance, a patch kit can be a quick and easy solution. These kits include a self-adhering mesh patch that simply sticks to the wall and covers the hole. The problem with this method, however, is that it can leave the hole slightly raised above the surrounding drywall.
For larger holes, the repair method is more complex and requires cutting out the damaged area and installing a new piece of drywall. This can be difficult to do on your own and is best left to professional technicians.
To repair a hole, first remove any loose gypsum or paper and clean the area. Then, use a putty knife to apply a thin layer of joint compound over the surface. Then, sand the compound until it is smooth and even. Finally, prime and paint the patch to match the rest of the wall.
When repairing a hole, it’s important to “feather” the edges of each application of compound, applying progressively finer grits of sandpaper as you go. This process helps the edge of the compound blend in with the surrounding wall and eliminates any obvious transitions or edges that might make the repaired area stand out from the rest of the wall.
Keeping an eye out for the signs of wear and tear in your home’s drywall is crucial to its longevity and overall health. From hairline cracks to water damage, addressing these signs promptly can help prevent them from escalating into major issues and keep your home safe and comfortable for years to come.
Nail Pops
There are few things more gratifying to a do-it-yourselfer than a flawless drywall job. But few things are more frustrating than nail pops, which occur when the point of attachment between drywall and wooden structural material (studs, joists, trusses) becomes loose. Basically, it happens when wood expands and contracts, shifting the drywall on the studs and pulling the mounting nails or screws out of place, creating a bump that looks like a round nail head sticking out of your wall. Nail pops are fairly common, and they can occur in a random spot or run along a drywall seam with several of them lined up in a row.
Nail pops can affect newer homes, too, but the problem is more likely to occur in older homes where different materials were used to secure drywall in place. For example, nails were commonly used to fasten drywall in old homes, while modern houses are typically built with drywall screws.
It is possible to fix a popped nail, although it may require some patience and a few extra tools. The first step is to locate the nail or screw. This can be done by running your hands over the drywall surface and feeling for any bumps. If you find one, circle it with a pencil to make it more obvious. Once you have located it, gently tap it with a hammer or a drill fitted with a screwdriver until the smooth shank of the nail or screw is re-seated below the drywall’s surface. It may take a few attempts to get it right and avoid damaging the drywall paper surface.
You may also use a drill to attach a drywall screw above and below the popped nail to reinforce the connection. This is a much better option than trying to pound a nail back into place, as this will almost always result in the drywall compound and paint being scuffed off of the underlying wood and causing further damage. Ultimately, nail pops are mostly cosmetic and not a sign of major foundation problems in your home. But if they are accompanied by other signs of foundation trouble, such as sticking windows and doors or diagonal cracking in brick walls, you should call a professional.
Water Damage
Unlike cracks and holes, water damage requires a different approach to drywall repair. Regardless of whether the water is caused by a leak, flood, or natural disaster, the source must be addressed and eliminated before repairs can be made. Once the water is gone, it’s important to allow the drywall to dry out completely before attempting any work.
In addition to addressing the water source, it’s also important to check for signs of mold growth. Mold thrives in damp areas such as bathrooms, kitchens, basements, attics, and crawl spaces. Mold growth can be difficult to spot, especially if it’s hidden under wallpapers or behind a crack in the wall.
After the drywall is thoroughly dry, it’s important to prime the area before touching up or repainting. This ensures that the patched area blends with the surrounding paint and provides a smooth, even appearance. If any blemishes are left behind after priming, they can be touched up with a dab of primer and painted over to hide them.
If you find that your drywall is damaged and needs to be repaired or replaced, you should call a drywall restoration company for help as soon as possible. They will be able to assess the severity of the damage and address any potential health risks that may occur from mold or other issues.
In some cases, you will need to replace the entire section of drywall. This is particularly true if it is wet or saturated, or if you find that the drywall is warping. In these situations, it’s best to contact a professional to avoid additional problems and prevent mold from forming. They will be able to assess the situation and recommend the proper steps to take for a quick, thorough repair job. They can also offer advice on how to prevent future drywall damage from occurring. This includes checking for any gutters that are clogged or not draining properly, and cleaning out your attic to prevent overflow and moisture buildup. It’s also recommended to have a dehumidifier in your home during rainy weather to reduce the amount of humidity in the house, which can cause drywall to rot or mold to grow.