Concrete Repair Bismarck is a critical process. It can improve safety and help prevent future damage.
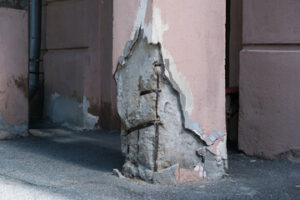
Experienced professionals are familiar with various products and techniques to best repair a structure. They know how to balance fast-curing materials with scheduling needs to minimize downtime.
Before starting the repair process, the surface should be swept and cleaned. Small cracks can be filled with hydraulic cement, which will expand as it dries.
Surface Repair
As concrete surfaces age, they may suffer from spalling, cracking, delamination and discoloration. If left untreated, these issues can quickly escalate into serious structural damage and costly repairs. It’s important to fix these problems as soon as possible, in order to reduce repair costs and ensure a safe environment for those who work on or around concrete structures.
Depending on the extent of surface damage, it may be necessary to use different concrete repair methods. For example, surface resurfacing can be an effective option for minor spalling. This involves cleaning the surface and then applying a high-quality concrete resurfacer to restore its appearance and protective qualities.
For more severe spalling or areas with significant cracking, a patching technique is often needed. This involves drilling holes across the length of a crack, and then injecting a fast-setting concrete repair material into the hole to fill in the crack and prevent further damage.
When using this type of concrete repair, it’s important to choose the correct package size for the amount of area that needs to be repaired. It’s also important to follow the manufacturer’s instructions for mixing, application and curing. This will help ensure the highest quality results and ensure that the repair will withstand any expected loads on the concrete.
Before starting any type of concrete repair, it’s important for workers to assess the environment and site conditions to make sure they’re prepared to begin. The temperature, moisture and other environmental factors can have a huge impact on the success of any concrete repair. For example, extremely hot temperatures can rapidly evaporate the water in the concrete, leading to improper curing and weak bonding. Conversely, low temperatures can slow the drying process, causing poor adhesion between the repair and the existing concrete.
It’s also important for workers to wear durable gloves, safety glasses and a dust mask when working on concrete repair projects. In addition, workers should use a low-VOC concrete repair product that’s designed to be environmentally friendly and safe for the health and well-being of everyone on the jobsite.
Structural Repair
Concrete is a great building material, but it does have some weaknesses. These are often caused by environmental factors like water seepage or chemical attacks, which can cause the concrete to deteriorate. Structural repair in concrete is a complex process and requires professional knowledge and experience to ensure the safety and durability of your structure.
Structural repair includes chipping and removing concrete in areas of spalling or deterioration, and replacing the damaged sections with new concrete. This work can also include tying in to existing reinforcing steel and concrete anchors to prevent future damage.
When repairing structural concrete elements, it is important that the replacement concrete be properly placed to ensure the structure can remain load bearing and perform as intended. This is particularly critical in deep repairs where the depth of the new concrete exceeds 6 inches. In these cases, the existing concrete should be removed to the proper depth and a bonding grout used in the replacement section.
Depending on the size and scope of the repairs, structural repair may include epoxy injection with or without added reinforcement. It may also involve drilling and plugging of concrete cracks, or the use of prestressing steel to add a compressive force to weak sections of concrete to strengthen them further.
In addition to structural repair, some concrete structures require post-tension repairs to improve their load-bearing capacity and enhance their performance. This type of work can be done with either tendons or cables that are placed within the concrete, and it provides better load distribution in the structure to reduce stresses and strains.
All concrete repair projects should be designed by a qualified engineer experienced in restoration. The design should be comprehensive and cover the entire scope of repairs, including the removal of existing concrete, inspection, and testing to determine the best course of action for each situation. The results of these tests will help to ensure that the repaired concrete is able to fully perform and that it is resistant to deterioration in the future. This will help to increase the life of your concrete and protect your investment.
Carbon Fiber Wraps
Carbon fiber is a lightweight, high-strength material that’s valued by engineers and preferred by car enthusiasts for its premium aesthetics. It’s also used to wrap parts of a vehicle to strengthen them and reduce maintenance requirements. Whether it’s for cars or construction projects, there are several ways that carbon fiber can be applied to concrete structures to strengthen them and improve their performance.
Often referred to as carbon fiber vinyl wrap, this type of film is usually PVC-based with an adhesive layer. It can be applied to the surface of a car’s original paint with the use of a special heat gun. It’s an excellent alternative to repainting, which can be much more expensive and time-consuming. The vinyl can also be easily removed at a later date if the owner decides that they want to revert back to their original color.
When it comes to concrete repair, carbon fiber is being increasingly used as a reinforcing material. Compared to steel and other traditional reinforcement materials, it has greater flexibility, better corrosion resistance, and a lighter weight. It’s also less susceptible to fatigue and has a higher load-bearing capacity.
Concrete damage can be a major problem, especially in structural applications such as bridges and buildings. Fortunately, proper care and regular inspections can help prevent these problems from escalating into costly repairs.
Common concrete issues include cracks, settlement and heaving, discoloration, and mold and stains. These may seem minor, but they can be a sign of serious underlying issues such as soil erosion, water intrusion, and corrosion of the reinforcing steel.
One method of repairing concrete damage is by wrapping it with a flexible, prefabricated FRP composite jacket. Lopez-Anido et al. [41] designed and tested a GFRP jacket that was wrapped around deteriorated piles. The results showed that the FRP jacket increased the axial load capacity of the piles by 31% and improved their durability. The flexural strength of the concrete was also enhanced by up to 74% when compared with unjacketed concrete. GFRP jackets have become an attractive rehabilitation solution for damaged concrete structures because of their high-strength, light-weight, and superior corrosion resistance properties.
Routing and Sealing
Concrete structures are subjected to a variety of environmental pressures including temperature, water, and chemical exposure. These pressures exert shear and bending forces that can damage the structural integrity of the concrete structure. When these forces are combined with tensile stresses caused by internal stress such as loading or movement of the structure, the results are cracking, spalling, or debonding. Using proper construction practices can help mitigate these damages. For example, a drainage system may be necessary to relieve excessive pressures under floors and behind walls. This can prevent structural failure and promote longevity in the life of the structure. Properly designed reinforcing systems can handle tension zones and bending stresses in structural concrete. Additionally, a crack stitching method can be used to repair major cracks and stop them from spreading by injecting epoxy into the cracks and filling them with concrete.
Routing and sealing in concrete repair is an industry-wide technique that is effective for dormant cracks. The process involves widening the crack with a router and then filling it with non-sag sealants or fillers like epoxies, silicones, and urethanes. This will help create a grout key, which locks the crack and helps reduce leakage in the future.
When performing this type of concrete repair, it is critical that the surrounding pavement is in good condition. To prepare for patching, it is recommended to remove any areas of deteriorated concrete and debris that are causing rutting or shoving. It is also crucial that the surrounding area is adequately moist-cured, as this will help to improve bonding of new and existing concrete.
To ensure proper placement of the patch, a bond coat can be applied to the surface before placing the concrete. This bond coat is made from a mixture of portland cement and sand and should be the consistency of whipped cream. The application of the bond coat will also help to reduce the risk of a freeze/thaw cracking problem.
Depending on the type of repair being performed, a longitudinal joint can be prepared for by placing a bond breaker along the length of the patch. This can be a simple fiberboard or other material that is flush with the longitudinal face of the repair and extends the full width of the patch for repairs over 4.5 m (15 ft). The use of wiggle bolts or tie bars is recommended when preparing longitudinal joints in slab replacements or repairs greater than 4.5 m.